Come portare i motori in corrente continua nell’era digitale
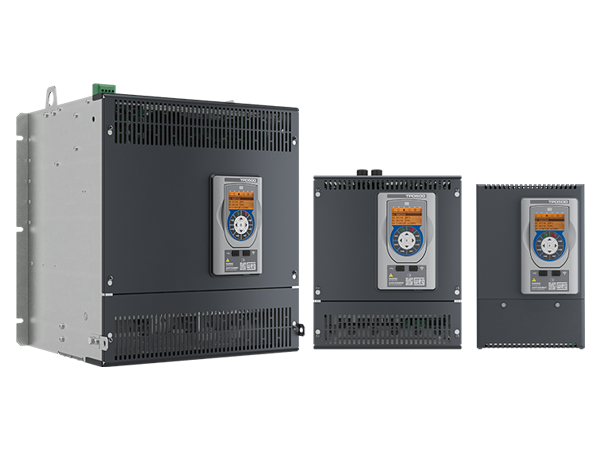
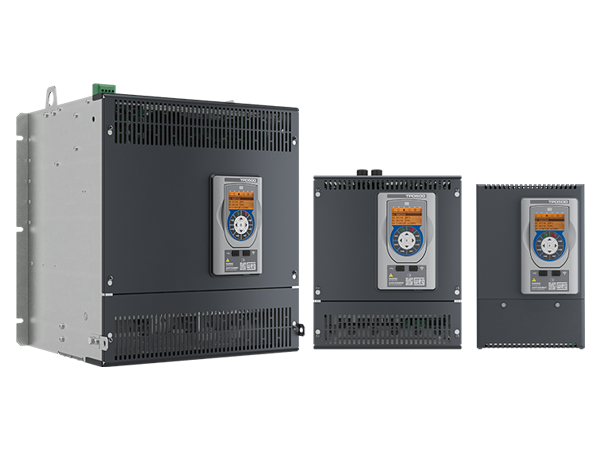
Perché le apparecchiature datate hanno ancora un ruolo nell’Industria 4.0 e come le nuove tecnologie di azionamento lo rendono possibile
“Non li fanno più come una volta”. Questo detto si adatta perfettamente all’industria pesante, dove i motori a corrente continua installati decenni fa garantiscono ancora prestazioni affidabili. Ma, con la digitalizzazione sempre più spinta, la vera sfida non è se i motori possano continuare a funzionare, bensì se l’infrastruttura che li supporta riesca a stare al passo. Andrea Verzaglia, Product Manager, e Umberto Del Grande, Responsabile del Dipartimento Marketing Prodotto di WEG, azienda specializzata in motori e azionamenti, spiegano come i nuovi approcci al controllo motore permettano alle apparecchiature tradizionali di prosperare nell’era dell’Industria 4.0.
In settori come quello dei metalli, delle materie plastiche, delle miniere e della carta, i motori a corrente continua rimangono un pilastro delle operazioni critiche. La loro coppia elevata a basse velocità e la capacità di funzionare a quattro quadranti li rendono particolarmente adatti ad applicazioni impegnative come laminatoi, estrusori, gru e avvolgitori. Molti di questi motori funzionano in modo affidabile da decenni e non mostrano segni di usura meccanica. La sfida non risiede nei motori in sé, ma nei sistemi di controllo che li supportano. Gli azionamenti più vecchi, spesso basati su piattaforme obsolete, sono sempre più incompatibili con le esigenze dell’attuale panorama industriale connesso e guidato dai dati. I loro limiti in termini di connettività, diagnostica e conformità li rendono un collo di bottiglia in sistemi
altrimenti robusti.
Esigenze moderne, infrastrutture datate
Con l’accelerazione della trasformazione digitale, le aspettative nei confronti dei sistemi di controllo motore si sono evolute. Gli ambienti industriali odierni richiedono azionamenti in grado di integrarsi perfettamente in reti di automazione più ampie. Lo scambio di dati in tempo reale con i PLC, la compatibilità con i protocolli basati su Ethernet e le soluzioni di sicurezza integrate sono diventate essenziali per soddisfare le esigenze dell’automazione moderna.
Purtroppo, molti sistemi di azionamento esistenti non sono costruiti per questo. L’assenza di opzioni di rete industriale come PROFINET o EtherNet/IP può impedire ai sistemi esistenti di partecipare alle configurazioni di automazione dell’intero impianto. Lo stesso processo di messa in servizio richiede spesso molto tempo e comporta l’inserimento manuale dei parametri o strumenti obsoleti che non dispongono di un feedback diagnostico moderno. In alcuni casi, anche il raggiungimento di funzionalità di base come l’accesso remoto o l’aggiornamento del firmware diventa un compito complesso.
Con l’aumento delle esigenze dei processi industriali, è sempre più importante garantire un’elevata efficienza e la conformità agli standard moderni. La distorsione armonica, in particolare nei sistemi ad alto carico, può introdurre gravi inefficienze, portare al degrado delle apparecchiature e aumentare il rischio di sanzioni da parte dei fornitori di servizi. Inoltre, molte soluzioni di azionamento mancano di funzioni di sicurezza oggi fondamentali, come Safe Torque Off o Safe Brake Control, soprattutto in applicazioni con interazione uomo-macchina o movimenti verticali.
Ripensare le strategie di revamping
Una soluzione possibile è la sostituzione completa del sistema, incluso il motore. Ma spesso non è praticabile. I motori in corrente continua sono di norma integrati in sistemi complessi e rivestono un ruolo cruciale nella produzione. Rimuoverli comporterebbe interventi meccanici, riprogettazione di impianti elettrici e sistemi di sicurezza, con fermi macchina troppo costosi per ambienti produttivi continui o ad alta produttività.
Una strategia più intelligente è modernizzare solo ciò che serve — tipicamente l’azionamento. Sostituendo l’azionamento, ma mantenendo il motore e l’impianto meccanico esistenti, si possono ottenere molti dei benefici di un sistema nuovo senza i costi e le interruzioni di una sostituzione completa. Questo consente anche di preservare gli investimenti fatti, adeguando al contempo l’impianto agli standard di prestazione e conformità attuali.
Nuove generazioni di azionamenti pronti per il revamping
Per rispondere a queste esigenze, è nata una nuova generazione di azionamenti in corrente continua progettati per superare i limiti delle soluzioni tradizionali. Questi dispositivi sono pienamente compatibili con apparecchiature esistenti, e possono essere installati senza modificare il layout dei quadri o la morsettiera.
Sotto un aspetto familiare, offrono funzionalità del tutto rinnovate:
- supporto multi-protocollo Ethernet per una perfetta integrazione con PLC moderni
- ambienti software intuitivi per la configurazione via USB, Ethernet o Wi-Fi
- diagnostica in tempo reale
- copia rapida dei parametri su più dispositivi e aggiornamenti firmware gestibili anche da remoto (sebbene richiedano ancora un certo grado di accesso fisico).
Questi azionamenti sono anche progettati per garantire alte prestazioni energetiche. In applicazioni ad alta potenza, la configurazione a dodici impulsi consente una significativa riduzione della distorsione armonica, migliorando l’efficienza energetica, prolungando la vita utile delle apparecchiature e contribuendo alla stabilità della rete elettrica. Soprattutto, includono funzioni di sicurezza direttamente nell’architettura di controllo. Funzionalità come Safe Torque Off e Safe Brake Control — essenziali in gru, paranchi e applicazioni con movimenti verticali — sono integrate nel drive, senza necessità di hardware esterno, semplificando la progettazione e favorendo la conformità agli standard come EN ISO 13849-1 e
IEC 61800-5-2.
Modernizzazione senza sostituzione: il caso TPD500
Un esempio concreto di questa nuova generazione è il TPD500 di WEG. Evoluzione del diffusissimo e collaudato TPD32-EV, il TPD500 è un convertitore AC/DC di nuova generazione, progettato per controllare motori in corrente continua in applicazioni industriali dove sono richieste alta coppia, basse velocità e massima affidabilità.
Il TPD500 è un sostituto diretto con ingombri e cablaggi identici, ideale per progetti di revamping dove è fondamentale mantenere quadro e motore esistenti. Integra una piattaforma di controllo digitale moderna, con supporto nativo per protocolli come Modbus TCP, tastierino di programmazione intelligente e strumenti software intuitivi che riducono i tempi di messa in servizio. La connettività wireless opzionale consente la configurazione e la diagnostica a distanza (particolarmente utile in impianti di grandi dimensioni o di difficile accesso).
Compatibile sia con funzionamento a due che a quattro quadranti, il TPD500 gestisce carichi gravosi con precisione. Per applicazioni su larga scala, sono disponibili soluzioni chiavi in mano fino a 3300 A, oppure solo l’unità di controllo, integrabile con ponti di potenza di terze parti fino a 20000 A.
Il design del convertitore AC/DC include anche una configurazione a dodici impulsi (disponibile entro l’anno) per minimizzare le armoniche nei sistemi ad alto carico. Sul fronte della sicurezza, le prossime funzionalità del TPD500 includeranno Safe Torque Off e Safe Brake Control, fondamentali in ambienti con movimentazione verticale o presenza di operatori.
Valorizzare e prolungare la vita degli impianti tradizionali
L’arrivo di azionamenti come il TPD500 rappresenta un cambio di paradigma nella gestione delle apparecchiature esistenti. Queste non sono più un ostacolo alla trasformazione digitale, ma diventano la base di sistemi modernizzati, in grado di coniugare l’affidabilità meccanica con il controllo e la connettività più avanzati.
È vero che non li fanno più come una volta, ma, nell’Industria 4.0, la possibilità di modernizzare senza sostituire diventa sempre più preziosa, scalabile e pronta per il futuro. Per saperne di più su come WEG supporta la modernizzazione dei motori in corrente continua con il Convertitore AC/DC TPD500, visita il sito ufficiale dell’azienda.
L'articolo Come portare i motori in corrente continua nell’era digitale sembra essere il primo su Meccanica News.
Qual è la tua reazione?






