I materiali avanzati potenziano la stampa 3D, ecco le innovazioni più interessanti
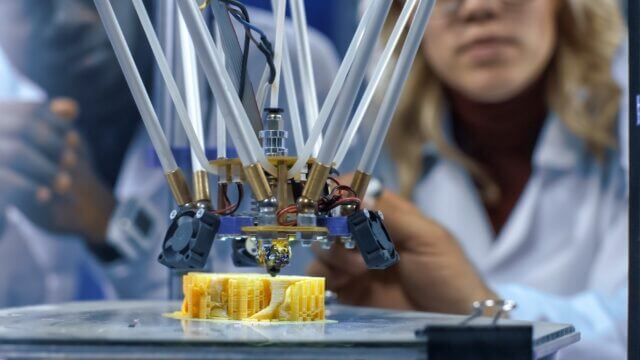
ADDITIVE MANUFACTURING
I materiali avanzati potenziano la stampa 3D, ecco le innovazioni più interessanti
La manifattura additiva sta vivendo una fase di profonda trasformazione grazie all’uso di materiali avanzati che consentono di superare i limiti tradizionali della stampa 3D. Oggi, oltre a realizzare forme complesse spesso impossibili da ottenere tramite tecniche sottrattive, l’additive manufacturing integra materiali non solo incredibilmente leggeri ma anche intelligenti, capaci di fornire funzionalità sensoriali e interattive. Un approccio che apre nuove opportunità in ambiti come il biomedicale, l’Internet of Things (IoT) e la manutenzione predittiva.
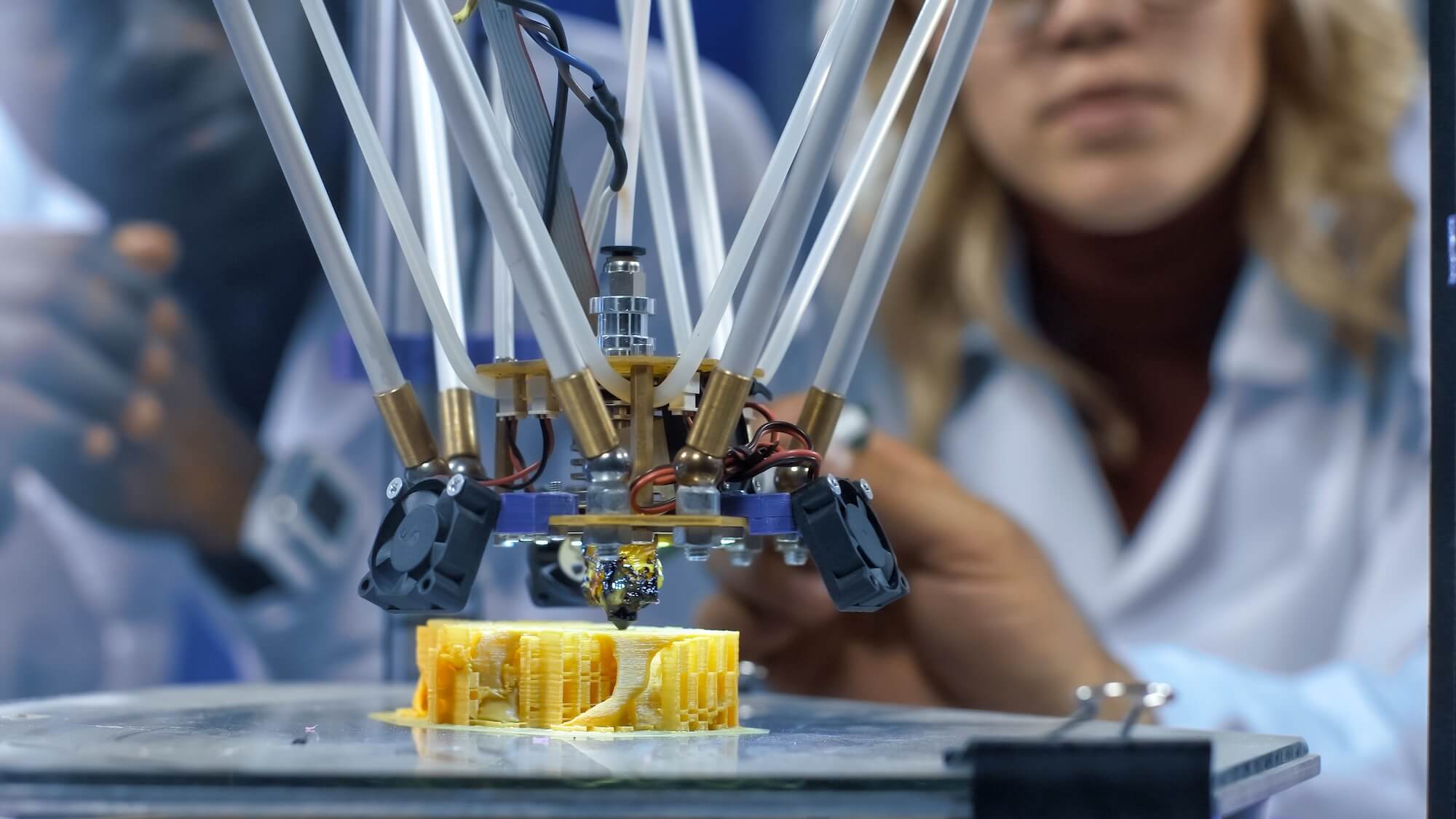
I materiali avanzati consentono di superare i limiti dei polimeri tradizionali grazie all’uso, tra gli altri, di nanotubi di carbonio, grafene e fibre composite. Questi materiali permettono di realizzare componenti più leggeri, resistenti e con caratteristiche specifiche come flessibilità o resistenza termica. Un esempio concreto è rappresentato dall’uso di leghe metalliche, tra cui citiamo l’Inconel 718, ampiamente adottata nell’ingegneria aerospaziale perché combina alta resistenza meccanica e capacità di rimanere inalterata a temperature estreme (700°C). Caratteristiche che consentono di produrre parti strutturali di aeromobili, veicoli spaziali, sistemi di propulsione, satelliti e attrezzature mediante stampa 3D metallica (laser powder bed fusion).
I materiali compositi CFRP (Carbon Fiber Reinforced Polymers), invece, utilizzati da aziende come Airbus, sono ottimi per ridurre il peso degli aeromobili, migliorandone l’efficienza energetica. Questi sono solo due esempi: i materiali avanzati stanno trovando sempre più applicazioni in numerosi settori industriali.
In questo articolo vedremo alcune delle soluzioni più interessanti già esistenti, i potenziali sviluppi della stampa 3D (possibili solo grazie ai materiali di ultima generazione) e le principali criticità legate alla loro adozione.
Le prestazioni superiori dei materiali avanzati
Tra le caratteristiche più interessanti dei materiali avanzati per l’additive manufacturing c’è quella della “sensibilità”. Un termine che nella stampa 3D indica la capacità dei materiali di rispondere a stimoli esterni come pressione, temperatura o deformazioni, trasformando così un componente stampato in un dispositivo intelligente.
Facciamo un breve esempio per chiarire: il progetto MISTICO del Politecnico di Milano ha sviluppato compositi piezoresistivi stampabili in 3D in grado di rilevare micro-fratture o variazioni strutturali nelle strutture, in tempo reale. Questi materiali permettono il monitoraggio continuo degli stati di salute dei componenti, ad esempio per tenere sotto controllo in maniera fine ponti o strutture robotiche.
Anche l’azienda italiana LATI3DLab ha sviluppato filamenti conduttivi come Alfaohm, che integrano nanotubi di carbonio nel PLA per produrre sensori stampati in 3D, applicabili all’interno di dispositivi diagnostici sofisticati e sistemi IoT.
Personalizzazione potenziata dai materiali funzionali
La stampa 3D, inoltre, può modulare localmente proprietà come rigidità, conducibilità o resistenza, integrando diverse funzionalità in un singolo componente attentamente progettato e disegnato. Questa possibilità apre scenari innovativi in ambiti come la robotica morbida e il biomedicale. Un esempio significativo è quello dell’azienda canadese Myant, che stampa tessuti intelligenti che integrano sensori biometrici per il monitoraggio posturale personalizzato. Tali sensori vengono impiegati utilizzati durante la riabilitazione di persone che hanno subito gravi incidenti o interventi chirurgici importanti.
In ambito protesico, realtà come Open Bionics realizzano protesi robotiche leggere, con feedback sensoriali stampati in 3D, in grado di migliorare il controllo motorio e la qualità di vita degli utenti.
Perché i materiali avanzati sono al centro dell’Industria 4.0
I materiali avanzati, in quanto intelligenti, facilitano la progettazione e lo sviluppo di un ecosistema produttivo integrato, dove sensoristica, digital twin e piattaforme cloud collaborano per ottimizzare progettazione, produzione e manutenzione. Aziende come Safran e Rolls-Royce, ad esempio, sfruttano queste tecnologie non solo per migliorare l’affidabilità delle componenti costruttive dei veicoli ma anche per accelerare lo sviluppo della produttività nel suo complesso.
Modelli di business innovativi come il design-as-a-service e la produzione on-demand, offerti da realtà come nTopology e Spare Parts 3D, permettono di ridurre stock e sprechi, rispondendo con flessibilità alle richieste di mercato. L’interoperabilità tra sistemi CAD, IoT e software di produzione è la chiave per realizzare questa visione di Industria 4.0, in cui la manifattura additiva diventa un processo intelligente e sostenibile.
Settori di applicazione dei materiali sensibili e intelligenti
I materiali sensibili trovano oggi ampio spazio in diversi settori industriali. Come abbiamo accennato uno di questi è il biomedicale, dove la stampa 3D è usata per realizzare dispositivi personalizzati, come protesi e ortesi con sensori biometrici integrati, che offrono un monitoraggio costante dei parametri fisiologici del paziente.
Nel campo dell’automotive e dell’aerospazio, le leghe metalliche intelligenti e le resine avanzate vengono impiegate per produrre componenti leggeri, resistenti e dotati di capacità di autodiagnostica, fondamentali per garantire sicurezza e prestazioni elevate. Inoltre, nel settore energetico, materiali come il grafene e i nanotubi di carbonio sono alla base di dispositivi per l’immagazzinamento energetico e supercondensatori.
Uno dei campi più promettenti è forse quello dell’Internet of Things, perché la stampa 3D sensoriale offre la possibilità creare componenti e dispositivi in grado di raccogliere e trasmettere dati in modo distribuito, aprendo nuove prospettive per la produzione intelligente e interconnessa.
Nanomateriali e nanotubi per l’Internet of Things
L’integrazione di nanomateriali conduttivi, come i nanotubi di carbonio, nei filamenti e nelle resine per la stampa 3D, dà alle aziende la possibilità di realizzare componenti in grado di modificare la propria conducibilità elettrica in risposta a stimoli meccanici, come pressione o deformazione. Come abbiamo anticipato questa proprietà conferisce agli oggetti stampati una funzionalità sensoriale, aprendo nuove opportunità nell’ambito dell’Internet of Things.
Nel campo della produzione di interfacce uomo-macchina e dispositivi indossabili ad esempio, il progetto 3DPRINTSAFE, promosso dal Fraunhofer Institute, ha sperimentato materiali compositi basati su nanotubi per creare superfici intelligenti capaci di rilevare tocchi, vibrazioni e pressioni.
Allo stesso modo, l’azienda Black Magic 3D ha sviluppato un filamento FDM semiconduttivo caricato con grafene, pensato per la prototipazione rapida di sensori flessibili e circuiti che vengono stampati direttamente sugli oggetti tridimensionali, senza bisogno di componenti esterni.
Negli Stati Uniti, l’innovativa tecnologia brevettata da Molecular Rebar Design consente di disperdere uniformemente nanotubi di carbonio in resine SLA/DLP, creando materiali semiconduttivi con prestazioni isotrope. Una soluzione ideale per sensori ESD e circuiti flessibili negli oggetti connessi, che contribuisce a una produzione digitale più intelligente e integrata.
Come la stampa 3D e i materiali avanzati stanno rivoluzionando la manutenzione predittiva
La manutenzione predittiva è una strategia chiave per aumentare l’affidabilità e la sicurezza degli impianti industriali e delle infrastrutture. La stampa 3D con materiali avanzati e sensibili dà alla manutenzione predittiva una marcia in più, permettendo la realizzazione di componenti intelligenti capaci di monitorare in modo continuo il loro stato e anticipare eventuali guasti.
La capacità di autodiagnosi integrata riduce la dipendenza da sensori esterni e consente interventi più rapidi e mirati, con benefici evidenti in termini di costi e efficienza.
Sensori integrati in componenti strutturali
Un esempio concreto di applicazione è offerto dal Fraunhofer IGCV, che ha sviluppato sensori integrati all’interno di componenti in fibra di carbonio (CFRP) stampati in 3D.
Questi sensori sono in grado di rilevare variazioni di tensione e microfratture, fornendo dati in tempo reale sulle condizioni di una struttura. Nel settore ferroviario e aeronautico, dove la sicurezza è imprescindibile, questa tecnologia permette di evitare guasti improvvisi e pianificare interventi di manutenzione con maggiore precisione, aumentando la durata dei componenti e riducendo i rischi operativi.
Monitoraggio distribuito di infrastrutture civili
Il Politecnico di Torino ha seguito un percorso parallelo a quello che abbiamo descritto prima, sviluppando materiali piezoresistivi stampabili in 3D capaci di monitorare strutture come ponti e viadotti in modo distribuito.
A differenza dei tradizionali sensori applicati esternamente, spesso costosi e difficili da installare, questi materiali sono integrati direttamente nella struttura durante la fase di produzione o manutenzione. Il risultato è una soluzione più economica e flessibile, che offre un monitoraggio continuo e localizzato, con importanti ricadute in termini di sicurezza e gestione del territorio.
L’integrazione con sistemi industriali avanzati
Il progetto DIAGON, frutto della collaborazione tra Università di Perugia e Consiglio Nazionale delle Ricerche (CNR), ha realizzato dispositivi stampati in 3D con materiali conduttivi in grado di segnalare condizioni critiche di stress o deformazione in tempo reale.
Questi sensori intelligenti si integrano con sistemi di controllo industriale come SCADA (Supervisory Control and Data Acquisition) e MES (Manufacturing Execution System), rendendo possibile un monitoraggio automatizzato e una gestione ottimizzata della manutenzione secondo i principi dell’Industria 4.0. Questi esempi raccontano quello che la manutenzione predittiva e la stampa 3D possono fare già oggi impiegando materiali avanzati.
Tutti i vantaggi della stampa 3D per la manutenzione predittiva
La possibilità di stampare componenti sensibili elimina la necessità di installare sensori esterni, riducendo significativamente i costi e semplificando la diagnostica. In contesti complessi, come impianti industriali modulari o infrastrutture distribuite, questa tecnologia dà l’opportunità di personalizzare i sistemi di monitoraggio sulla base di specifiche esigenze progettuali e operative.
L’approccio modulare favorisce inoltre la scalabilità e l’aggiornamento continuo degli impianti, per una manutenzione predittiva sempre più efficace e integrata.
Materiali evoluti per la salute dell’uomo e una medicina personalizzata
La manifattura additiva ha rivoluzionato il settore biomedicale. Oggi possiamo realizzare dispositivi su misura che non solo si adattano perfettamente all’anatomia del paziente, ma integrano anche funzionalità avanzate per migliorare l’interazione con il corpo umano e la raccolta dati in tempo reale.
La combinazione di personalizzazione e tecnologia sensoriale apre nuovi orizzonti per la cura e la riabilitazione, aumentando l’efficacia terapeutica e la qualità della vita. Come nell’esempio delle protesi robotiche e dei sensori biometrici di uno dei paragrafi precedenti.
Cerotti intelligenti stampati in 3D
Presso la Technische Universität di Vienna (TU Wien), un team di ricerca ha sviluppato un cerotto intelligente stampato in 3D che può monitorare parametri fisiologici come temperatura, idratazione e pH cutaneo in tempo reale.
Il dispositivo è realizzato con materiali biocompatibili e sensori stampabili in grafene, direttamente integrati nella struttura flessibile del cerotto. Questo tipo di tecnologia, ancora in fase prototipale, rappresenta un grande passo avanti nella cura delle ferite croniche e nel monitoraggio domiciliare di pazienti con patologie dermatologiche o metaboliche.
Guanti sensorizzati per la riabilitazione neuromotoria
Nell’ambito della riabilitazione, il progetto ManoBot dell’Università di Cagliari ha realizzato guanti sensorizzati, sfruttando stampa 3D e materiali piezoresistivi, capaci di rilevare i movimenti delle dita con elevata precisione. Il dispositivo è pensato per pazienti con deficit neuromotori e si interfaccia con software di analisi del movimento per personalizzare gli esercizi terapeutici.
I materiali usati, flessibili e leggeri, garantiscono comfort e aderenza, mentre la stampa additiva attua un adattamento morfologico su misura per ciascun paziente.
Impianti cocleari personalizzati: la via aperta da MED-EL
Nel campo degli impianti uditivi, l’azienda austriaca MED-EL ha sperimentato con successo l’uso della stampa 3D per produrre impianti cocleari altamente personalizzati, modellati sulla specifica anatomia dell’orecchio interno di ciascun paziente.
Grazie alla scansione TC (Tomografia Computerizzata) e alla manifattura additiva, si possono realizzare dispositivi con una precisione micrometrica, che migliorano la trasduzione del suono e riducono il rischio di danni tissutali. Questo è un altro caso in cui i materiali avanzati applicati alla stampa 3D garantiscono risultati terapeutici superiori.
Internet of Bodies: dispositivi connessi interagiscono con il corpo umano
La sinergia tra stampa 3D e materiali avanzati sta tracciando la strada verso l’Internet of Bodies (IoB), un ecosistema in cui dispositivi intelligenti, sensori biometrici e protesi connesse comunicano in modo integrato con l’organismo umano.
L’IoB promette di rivoluzionare la medicina personalizzata, la prevenzione e il monitoraggio continuo, grazie a tecnologie capaci di raccogliere e analizzare dati biologici in tempo reale, migliorando la salute e il benessere complessivi.
Nuovi modelli collaborativi nella manifattura additiva
La manifattura additiva non è una tecnologia che opera in modo “isolato”: man mano che si sviluppa, al contrario, si integra sempre più in un ecosistema digitale complesso che coinvolge progettazione, simulazione, produzione e manutenzione. Al centro di questa trasformazione ci sono le piattaforme collaborative e i gemelli digitali, che permettono di creare un flusso di dati continuo e condiviso, fondamentale per ottimizzare ogni fase del ciclo produttivo.
Software avanzati per la progettazione e la simulazione
Strumenti come Siemens NX, PTC Creo e Ansys Additive Suite rappresentano oggi il cuore della progettazione digitale per la stampa 3D. Questi software consentono di sviluppare modelli con sensori integrati in grado di monitorare in tempo reale parametri come vibrazioni, stress e temperatura durante la produzione e l’uso del componente. L’integrazione di questi dati nel cosiddetto “gemello digitale” consente di migliorare costantemente il singolo progetto, anticipare possibili problemi e ottimizzare la manutenzione predittiva.
Nuovi modelli di business
La digitalizzazione della manifattura additiva sta dando forma a modelli produttivi completamente nuovi, come il design generativo e la produzione on-demand erogata come servizio. Un esempio interessante è quello di Trinckle, software tedesco che offre la personalizzazione automatica di componenti meccanici o medicali partendo da dati parametrici o scansioni 3D, con flussi API che si integrano direttamente nei sistemi aziendali. Startup come Castor offrono piattaforme in cloud che analizzano grandi volumi di componenti industriali per identificare in modo automatico quali sono adatte alla stampa 3D, generando stime su costi, tempi e impatto ambientale.
Questa logica si estende anche alla supply chain: aziende come DB ESG, operativa nel settore ferroviario britannico, collaborano con hub di stampa locali per produrre componenti certificati su richiesta, direttamente vicino al luogo di installazione. Un approccio che taglia tempi di fermo macchina, elimina scorte statiche e rende la manutenzione più rapida ed efficiente, ridisegnando l’intero ciclo di vita del prodotto in ottica digitale.
Per realizzare pienamente queste opportunità, è essenziale garantire l’interoperabilità tra diversi sistemi digitali: CAD per la progettazione, piattaforme IoT per il monitoraggio, sistemi PLM/ERP per la gestione aziendale e le tecnologie di stampa 3D per la produzione. Solo attraverso un’integrazione fluida e un ciclo di feedback continuo è possibile abilitare una produzione intelligente, flessibile e orientata alla qualità.
Limiti e criticità nella stampa 3D con materiali funzionali
La stampa 3D con materiali funzionali rappresenta una delle frontiere più avanzate della manifattura additiva, ma il suo pieno potenziale è ancora ostacolato da alcune sfide tecnologiche e operative. Sebbene i materiali innovativi come polimeri caricati con nanotubi di carbonio, leghe metalliche ad alte prestazioni e compositi intelligenti abbiano aperto nuovi scenari applicativi, la loro gestione richiede un controllo estremamente rigoroso dei processi per garantire le proprietà desiderate e l’affidabilità dei componenti prodotti.
La complessità della sensibilità dei materiali avanzati
Uno degli aspetti più interessanti è allo stesso tempo anche uno dei più critici: la sensibilità intrinseca di questi materiali, ovvero la loro reattività a variazioni anche minime nei parametri di stampa, come temperatura, velocità di deposizione, pressione del laser o tempo di polimerizzazione, può creare risultati indesiderati. Piccoli cambiamenti possono compromettere la distribuzione delle particelle conduttive o delle fibre rinforzanti all’interno del materiale, alterando significativamente le proprietà meccaniche, elettriche o sensoriali del componente finito.
Ad esempio, nella stampa di polimeri caricati con nanotubi di carbonio o grafene, un’errata omogeneità nella dispersione dei nanomateriali può causare punti di debolezza o variazioni nella conducibilità elettrica, compromettendo la funzionalità di sensori embedded o elementi strutturali.
Requisiti di processo per i materiali di frontiera
Tra i materiali più complessi da gestire vi sono le leghe metalliche come l’Inconel 718, che abbiamo già citato, usate in ambiti come quello aerospaziale per la loro elevata resistenza e stabilità termica. La lavorazione di queste leghe tramite tecniche come il laser powder bed fusion richiede parametri di processo finemente calibrati per evitare difetti quali porosità, deformazioni o stress residui che possono compromettere la durata e la sicurezza delle parti.
Analogamente, i compositi con sensori embedded, che integrano materiali conduttivi o piezoresistivi, necessitano di condizioni di stampa stabili e ripetibili per mantenere le proprietà funzionali senza degradare le capacità sensoriali.
Tecnologie di monitoraggio e controllo qualità
Per affrontare queste criticità, le aziende del settore come EOS, GE Additive e Trumpf hanno sviluppato sistemi di stampa 3D dotati di sensori integrati, capaci di monitorare in tempo reale parametri termici, acustici e visivi durante il processo produttivo. Questi sistemi avanzati di sensoristica in-process permettono di rilevare anomalie, correggere deviazioni e garantire la qualità e la ripetibilità dei componenti, elementi imprescindibili soprattutto per applicazioni critiche in settori come aerospazio, biomedicale e automotive.
Questi controlli automatici sono parte integrante di un approccio “closed loop” che permette di chiudere il ciclo di feedback tra progettazione, produzione e controllo qualità, elevando la produzione additiva a standard industriali di alto livello.
Il futuro dei materiali avanzati nella manifattura additiva
I materiali avanzati sono legati a doppio filo all’evoluzione della stampa 3D e aprono nuove prospettive per la produzione industriale intelligente, personalizzata e sostenibile. Grazie alle loro proprietà funzionali e sensoriali, abilitano componenti capaci di interagire con l’ambiente, favorendo l’adozione di modelli di manutenzione predittiva e integrazione con sistemi IoT. Le sfide tecnologiche, come il controllo rigoroso dei processi e l’omogeneità dei materiali, spingono a una crescente collaborazione tra ricerca accademica e industria, accelerando l’innovazione nel settore. L’adozione sempre più diffusa di piattaforme digitali integrate e l’interoperabilità dei sistemi sono elementi chiave per realizzare pienamente il potenziale dei materiali avanzati.
L'articolo I materiali avanzati potenziano la stampa 3D, ecco le innovazioni più interessanti proviene da Innovation Post.
Qual è la tua reazione?






